https://e.ate.wpml.org/dashboard?id=122792806&language=fa
A preform is a plastic component produced through the injection molding process. It is cylindrical in shape and undergoes a blow molding process to be transformed into bottles or containers. Typically made from polyethylene terephthalate (PET), preforms are used as the primary raw material for manufacturing a wide range of plastic bottles, including those for beverages, oils, and cleaning products.
Key Features of Preforms:
High Transparency: Provides a clear and visually appealing appearance, ideal for showcasing beverages.
Mechanical Durability: Capable of withstanding pressure and impact.
Lightweight: Reduces transportation costs, making it economically efficient.
Recyclability: Environmentally friendly, supporting sustainable practices.
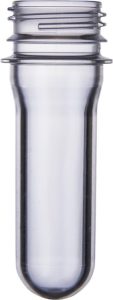
The Bottle Production Process from Preforms
1. Preform Heating: Preforms are heated in specialized machines to become soft and moldable.
2. Mold Placement: The softened preform is placed inside a mold.
3. Stretching the Preform: Using a stretch rod, the preform is elongated within the mold while pre-blowing inflates it slightly.
4. Air Blowing: High-pressure air is used to expand the preform into the mold’s shape.
5. Cooling: The formed bottle is cooled within the mold to retain its final shape.
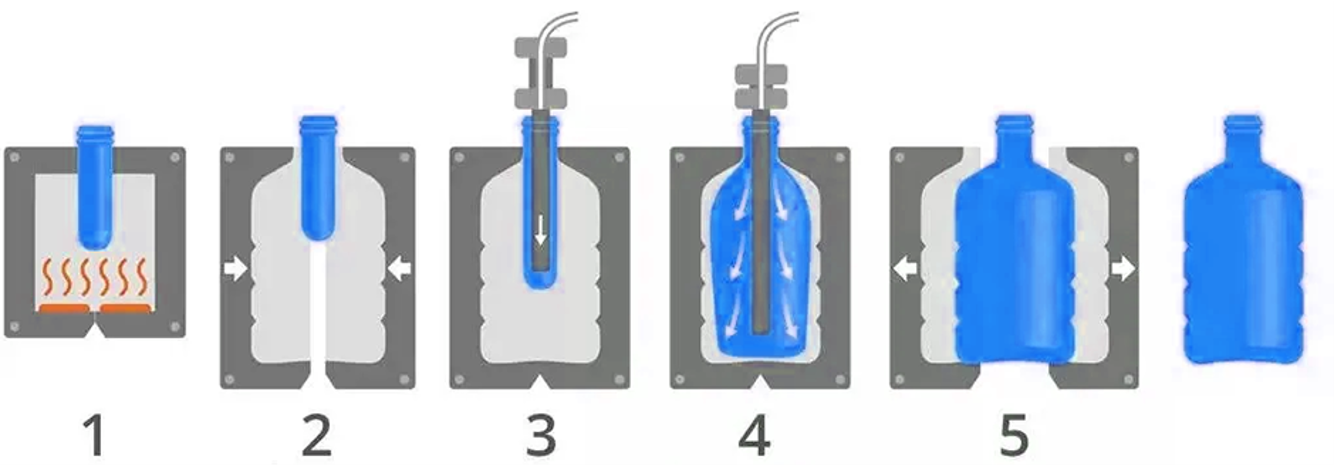
Applications of Preforms in Various Industries
Beverage Industry: Used for producing bottles for mineral water, soft drinks, and juices.
Pharmaceutical Industry: Ideal for packaging liquid medicines due to their hygienic and safety standards.
Food Industry: Suitable for edible oils, sauces, and similar products.
Cosmetics and Hygiene Products: Used for packaging shampoos, lotions, and other personal care items.
How to Choose the Right Preform?
When selecting a preform, the following factors are crucial:
Weight: Lighter preforms are ideal for products like water, while heavier ones are better for oils.
Neck Size: Ensure compatibility with the cap and closure system.
Transparency and Quality: High clarity is essential for beverage bottles to appeal to consumers.
Neck Finish of Preforms
The neck finish refers to the top section of the preform where the bottle cap is attached. This area is critical for ensuring a secure seal, preventing leakage, and providing structural integrity. Different neck finishes are available to meet specific requirements.
Factors Influencing Neck Finish Selection
Product Type and Viscosity: Tailored for specific uses, such as carbonated drinks, oils, or non-carbonated beverages. •
Cap and Closure System: Must match the neck finish for effective sealing.
Production Method: The manufacturing process impacts the type of neck finish used.
Bottle Design: The neck finish should align with the overall aesthetic and functional design.
Capacity and Storage Conditions: Considerations for transportation and shelf life.
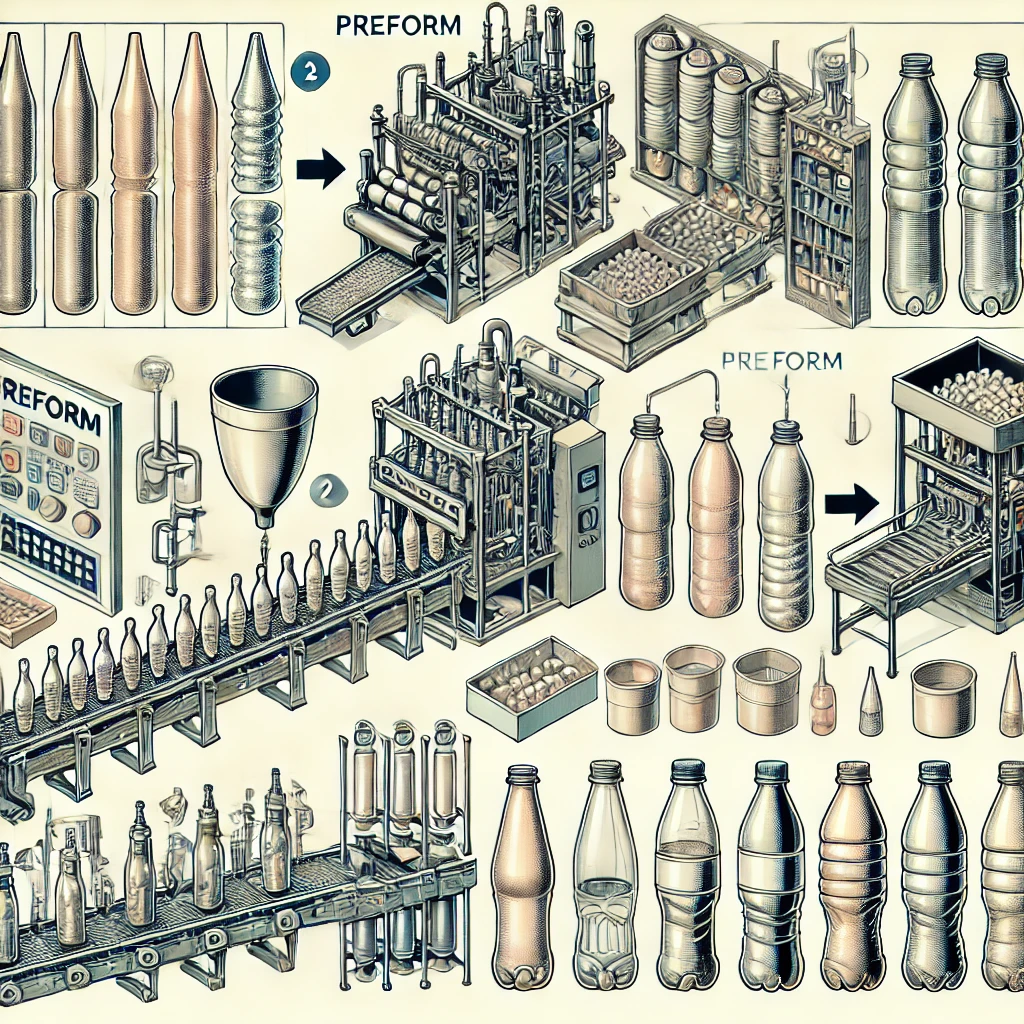
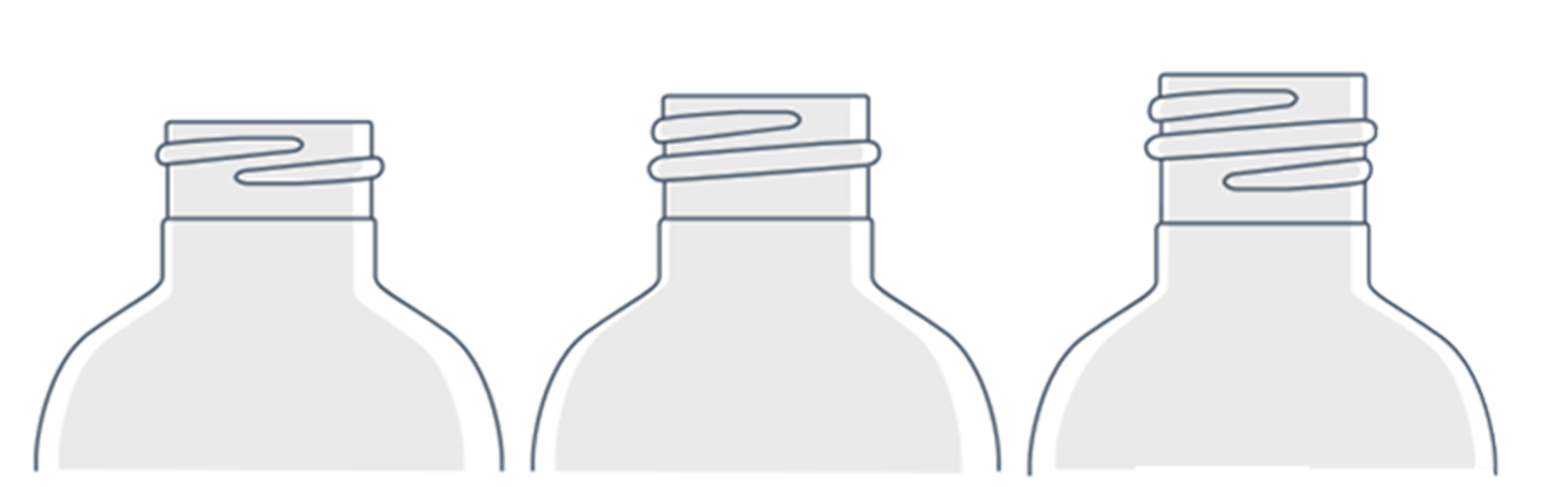
Guide to Preform Neck Types
Type
Usage
Weight
28 Pco 1881
Single start
Thread turn 720
All carbonated beverages and sodas are packaged with short neck caps.
3.8 gr
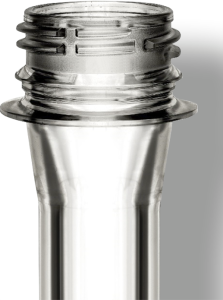

BPF-C 28
Single start
Thread turn 720
Carbonated Beverages
All sodas, lemonades, and other drinks.
lemonades
Other Drinks
6.1 gr


PCO Corvaglia 28
Single Start
°744 Thread turn
Carbonated Beverages
All sodas
lemonades
Other Drinks
3.6 gr
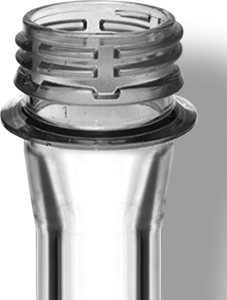

Alaska 26.75
Start 3
°120 Thread turn
Types of Liquid Oils
Types of Iced Tea
Energy Drinks
Carbonated Drinking Water
Drinking water
3.6 gr


Low 30.25
Start 3
°120 turn
Types of Liquid Oils
Types of Iced Tea
Energy Drinks
Carbonated Beverages
Drinking water
3.7 gr
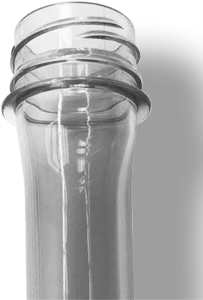
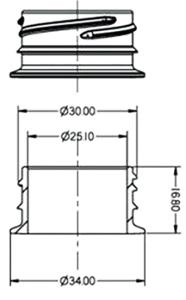
High 30.25
Start 3
°120 Thread turn
Drinking Water
Types of Iced Tea
Energy Drinks (Low Internal Pressure)
Drinking water
3.9 gr
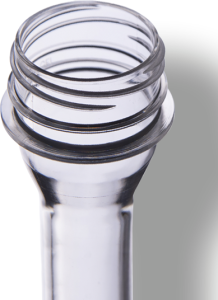
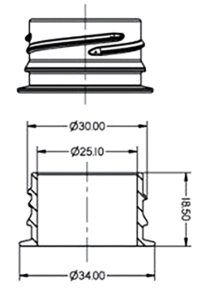
High 29.25
Start 3
°120 Thread turn
Types of Non-Carbonated Beverages
Drinking water
2.5 gr
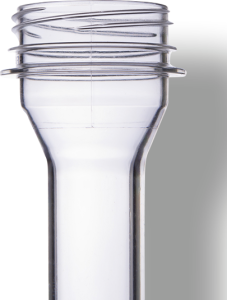
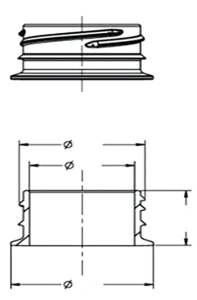
28 Pco 1810
Single start
Thread turn 720
All Carbonated Beverages and Sodas
5.1 gr

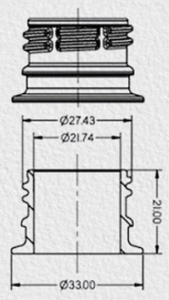